Introducción
La industria del cemento es una de las principales responsables de las emisiones globales de carbono. Un área con un potencial significativo de mejora es el almacenamiento de cemento, en particular el uso de silos de clínker. El clínker es el ingrediente principal del cemento y debe almacenarse en grandes volúmenes antes de su molienda y envasado final. Los silos de clínker tradicionales consumen mucha energía para funcionar y mantienen altas temperaturas que aceleran la liberación de carbono. Las nuevas tecnologías para el diseño de silos de clínker prometen mejorar la sostenibilidad en toda la cadena de suministro de cemento. En esta publicación del blog se analizará cómo la tecnología de silos de clínker afecta a la sostenibilidad en la industria del cemento y se analizarán algunas soluciones innovadoras que están surgiendo en este campo.
Desafíos del almacenamiento de clínker
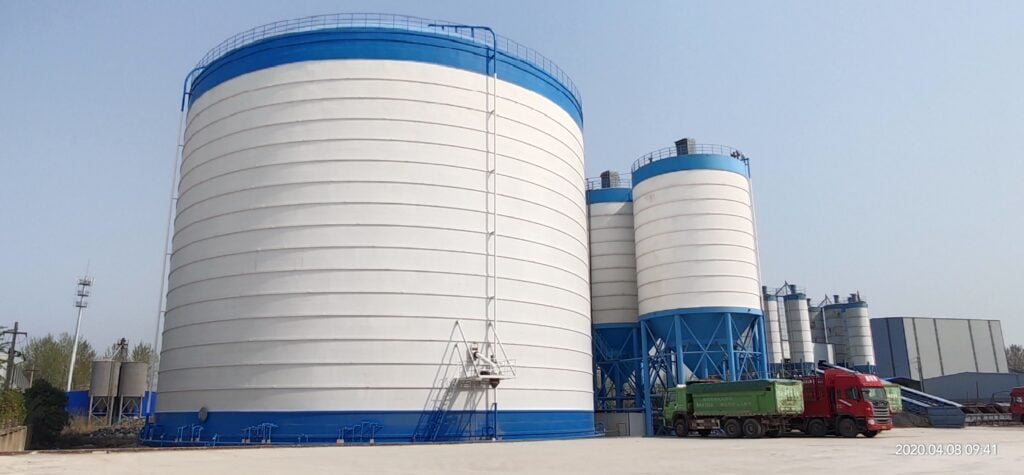
El almacenamiento de grandes volúmenes de clínker plantea varios desafíos desde una perspectiva ambiental. El clínker se produce a temperaturas de alrededor de 1450 °C y se enfría lentamente a medida que se transporta desde el horno hasta el almacenamiento. Los silos de clínker tradicionales no están bien aislados, lo que permite una pérdida excesiva de calor que desperdicia energía. El clínker caliente también continúa liberando dióxido de carbono a medida que se enfría, lo que contribuye a generar miles de toneladas de emisiones adicionales al año en las grandes plantas de cemento. Mantener las altas temperaturas dentro de los silos de clínker también requiere un importante aporte de energía para el calentamiento y el control de la temperatura. Las fugas de aire caliente y polvo de los silos convencionales agravan estas ineficiencias.
El almacenamiento adecuado del clínker también es importante para garantizar una calidad constante para la molienda final del cemento. Las variaciones de temperatura y la absorción de humedad pueden afectar la molturabilidad y el rendimiento del producto terminado si el clínker no se mantiene uniforme. Esto requiere un movimiento y mezcla frecuentes del clínker, generalmente a través de sistemas mecánicos como cajones, transportadores de tornillo o líneas de transporte de aire conectadas a los silos. El uso de energía y los costos de mantenimiento de estos sistemas internos de manipulación del clínker son otro factor en el huella de carbono de instalaciones de almacenamiento.
Tecnología de silos de clínker
Los avances en el diseño de silos de clínker tienen como objetivo abordar estos desafíos operativos y de sostenibilidad. Varias tecnologías emergentes se centran en mejorar el aislamiento, reducir las fugas de aire y minimizar el movimiento interno del clínker. Por ejemplo, algunos nuevos modelos de silos incluyen:
- Sistemas de aislamiento multicapa de gran espesor capaces de mantener el clínker a una temperatura media entre 10 y 15 °C más baja que los diseños tradicionales, lo que reduce significativamente las emisiones de carbono derivadas del enfriamiento del clínker.
- Tecnologías de sellado avanzadas alrededor de puntos de acceso, juntas y escotillas de inspección que logran fugas de aire cercanas a cero incluso bajo cambios de presión y expansión/contracción térmica.
- Mayores capacidades de silos y diseños optimizados para la “estratificación” natural del clínker durante el almacenamiento para promover la uniformidad de la temperatura con poca mezcla requerida.
- Monitoreo automático de temperatura y sistemas de calefacción local para controlar con precisión los puntos críticos y evitar fluctuaciones de temperatura en los silos.
Silo de Clinker vs. Modelo tradicional:
Mejoras de rendimiento | Nuevas tecnologías de silos de clínker en comparación con los modelos convencionales |
---|---|
Sellado mejorado | Las tecnologías más nuevas ofrecen mecanismos de sellado mejorados para minimizar la entrada de aire y evitar la humedad, lo que reduce el riesgo de degradación del clínker y garantiza la calidad del producto. Los modelos convencionales pueden tener un sellado menos eficaz, lo que genera mayores niveles de contaminación y pérdida de material. |
Monitoreo avanzado | Las tecnologías más nuevas de silos de clínker están equipadas con sistemas de monitoreo avanzados, que incluyen sensores y capacidades de análisis de datos en tiempo real, lo que permite una gestión precisa del inventario y un mantenimiento proactivo. Los modelos convencionales pueden depender de inspecciones manuales y carecer de un monitoreo integral, lo que genera ineficiencias y posibles riesgos. |
Integración de automatización | Las tecnologías más nuevas se integran perfectamente con los sistemas de automatización, lo que permite la operación remota, el manejo automatizado de materiales y la programación de mantenimiento predictivo. Los modelos convencionales pueden tener capacidades de automatización limitadas, lo que requiere más intervención manual y aumenta el riesgo de errores y tiempo de inactividad. |
Funciones de seguridad mejoradas | Las tecnologías más nuevas de silos de clínker priorizan la seguridad con características como un diseño estructural mejorado, sistemas de apagado de emergencia y protocolos de seguridad integrales. Los modelos convencionales pueden tener características de seguridad obsoletas o carecer de medidas de seguridad sólidas, lo que plantea riesgos para el personal y las operaciones. |
Mayor capacidad de almacenamiento | Las tecnologías más nuevas permiten capacidades de almacenamiento mayores y configuraciones más flexibles, que se adaptan a las crecientes demandas de producción y optimizan el uso del espacio. Los modelos convencionales pueden tener una capacidad de almacenamiento limitada y diseños rígidos, lo que limita la escalabilidad y la eficiencia de la producción. |
Estudio de caso
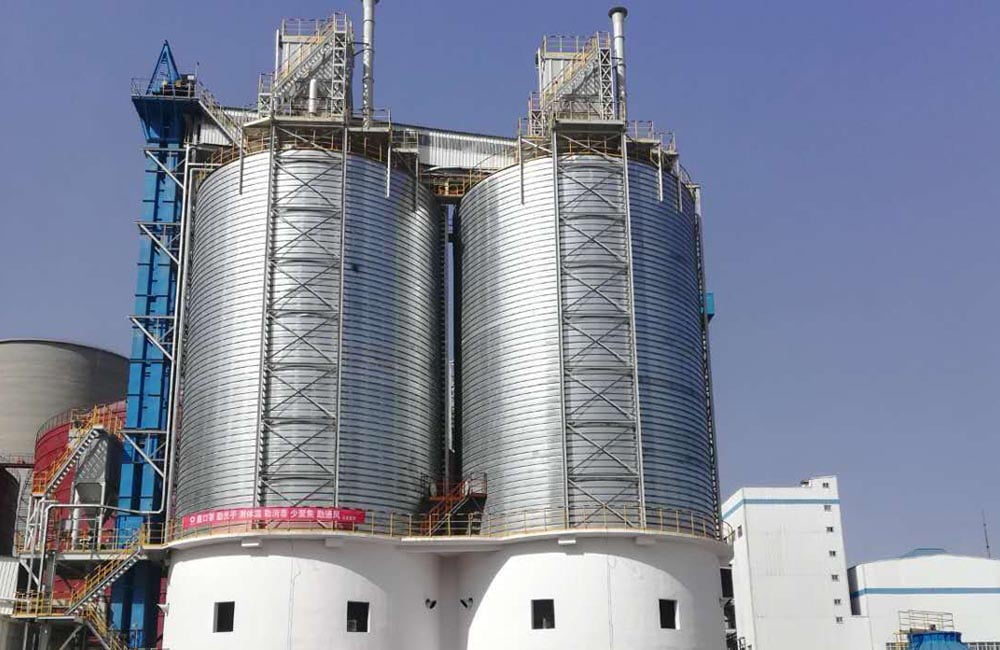
Almacenamiento sostenible de clínker en China Un productor de cemento que está logrando importantes avances en materia de sostenibilidad gracias a las mejoras en los silos de clínker es Anhui Conch Cement, el mayor fabricante de cemento de China. La empresa se enfrentaba a un aumento de los costes energéticos y de los impuestos sobre el carbono en muchas de sus instalaciones. Un proyecto prioritario consistía en sustituir los antiguos silos de clínker de su planta de Hefei, capaces de almacenar hasta 100.000 toneladas.
Un análisis determinó que los silos de circuito abierto existentes perdían aproximadamente entre 15 y 20 °C de calor por día a causa del clínker, lo que desperdiciaba una cantidad significativa de energía térmica. El polvo y el calor fugitivos también afectaban a las comunidades circundantes. Para abordar estos problemas, Conch Cement instaló dos nuevos silos cerrados de un proveedor líder que cuentan con sistemas de aislamiento avanzados, sellado hermético y control de temperatura automatizado.
Después de un año de funcionamiento, los nuevos silos de clínker han mantenido una reducción media de 10 °C en la pérdida de temperatura en comparación con antes. Esto se traduce en un ahorro energético anual de 5.000 megavatios hora gracias a la reducción de las necesidades de recalentamiento (la energía equivalente a la que consumen 500 hogares en China durante un año). Las emisiones de dióxido de carbono también se redujeron en 4.000 toneladas. Los directores de la planta han logrado que las operaciones sean ininterrumpidas y que se cumpla más fácilmente con las normas de emisiones más estrictas. En general, el proyecto logró una amortización de dos años y ha marcado la pauta para las mejoras en el almacenamiento de clínker en las extensas operaciones de Conch Cement.
Conclusión
Mientras la industria del cemento trabaja para reducir su huella de carbono, las innovaciones en el almacenamiento de clínker presentan una oportunidad significativa. Las nuevas tecnologías de silos que cuentan con aislamiento avanzado, sellado hermético y control automático de la temperatura permiten importantes ahorros de energía al minimizar las pérdidas de calor durante el enfriamiento y almacenamiento del clínker. Los estudios de casos muestran que las actualizaciones de los silos de clínker pueden lograr una rápida amortización de dos años o menos solo por la reducción de costos de energía. Cuando se combina con ganancias de eficiencia continuas en las operaciones de molienda, horno y otras áreas, el almacenamiento optimizado de clínker ayuda a los productores de cemento a realizar la transición a prácticas de producción más sostenibles. A medida que las regulaciones sobre el carbono se endurecen en todo el mundo, la tecnología de silos de clínker seguirá avanzando para respaldar la transición hacia prácticas de producción bajas en carbono de la industria.
Preguntas frecuentes
P: ¿Cuál es la vida útil típica de un silo de clínker?
R: Con un mantenimiento adecuado, un silo de clínker bien diseñado puede durar entre 25 y 30 años en promedio antes de que sea necesario reemplazar los componentes principales, como la carcasa o los sistemas de aislamiento. Algunos factores críticos que influyen en la vida útil incluyen la selección del material, la calidad del sellado/soldadura, la estabilidad del control de temperatura y la frecuencia del movimiento del clínker.
P: ¿Cómo se selecciona el tamaño adecuado de silo para una planta de cemento?
R: El tamaño del silo de clínker depende de la capacidad de producción diaria o anual de la planta y de los objetivos de inventario de clínker. Es habitual proporcionar una capacidad de almacenamiento de entre 7 y 10 días para equilibrar las operaciones del horno con las necesidades de molienda y envasado. Otros factores incluyen la densidad aparente del clínker, las tasas de recuperación de la base y el espacio disponible en la instalación. Los consultores de ingeniería con experiencia pueden ayudar a optimizar el tamaño.
P: ¿Qué mantenimiento requieren los silos de clínker?
R: El mantenimiento de rutina generalmente implica inspecciones regulares de la carcasa para detectar grietas o defectos, pruebas de integridad de sellos o juntas y lubricación o reemplazo de cualquier pieza interna móvil, como cajones o válvulas. Los sistemas de monitoreo de temperatura también necesitan calibración. Un mantenimiento más profundo, como la renovación del aislamiento o el reemplazo de las escaleras de acceso, puede realizarse cada 7 a 10 años, según el uso. Un mantenimiento adecuado es fundamental para maximizar el rendimiento y la vida útil del silo.